Services
Building Flow Design AB
The fundamental basis of almost all CFD problems are the Navier–Stokes equations, which define any single-phase (gas or liquid, but not both) fluid flow. These equations can be simplified by removing terms describing viscous actions to yield the Euler equations. Further simplification, by removing terms describing vorticity yields the full potential equations. Finally, for small perturbations in subsonic and supersonic flows (not transonic or hypersonic) these equations can be linearized to yield the linearized potential equations.
Historically, methods were first developed to solve the linearized potential equations. Two-dimensional (2D) methods, using conformal transformations of the flow about a cylinder to the flow about an airfoil were developed in the 1930s.
One of the earliest type of calculations resembling modern CFD are those by Lewis Fry Richardson, in the sense that these calculations used finite differences and divided the physical space in cells. Although they failed dramatically, these calculations, together with Richardson's book "Weather prediction by numerical process", set the basis for modern CFD and numerical meteorology. In fact, early CFD calculations during the 1940s using ENIAC used methods close to those in Richardson's 1922 book.
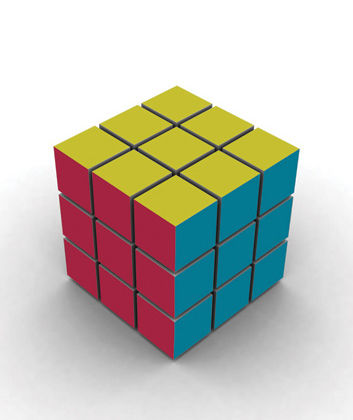
I'm a paragraph. Click here to add your own text and edit me.
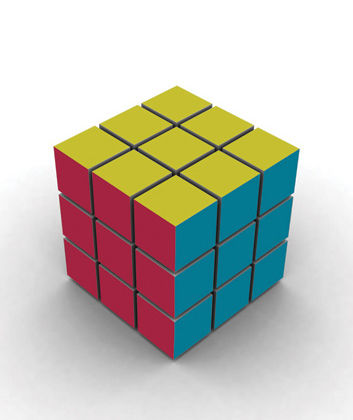
I'm a paragraph. Click here to add your own text and edit me.
Building Flow Design AB
Thermal Comfort
In fluid mechanics, multiphase flow is a generalisation of the modelling used in two-phase flow to cases where the two phases are not chemically related (e.g., dusty gases) or where more than two phases are present (e.g., in modelling of propagating steam explosions).
The momentum equation for each phase is less straightforward. It can be shown that a common pressure field can be defined and that each phase is subject to the gradient of this field, weighted by its volume fraction. Transfer of momentum between the phases is sometimes less straightforward to determine, and, in addition, a very light phase in bubble form has a virtual mass associated with its acceleration. (The virtual mass of a single bubble is about half its displaced mass).
Low-temperature Heating
The transient rotor–stator capability resolves the true transient interaction between components for maximum accuracy. It can be applied to individual pairs of blade passages or to the entire 360-degree machine. Setup and use is as simple as it is with the other frame-change models, and it is possible to combine transient and steady-state frame change interfaces in the same computation. Complementing this is the inclusion of second-order time differencing, which delivers greater transient accuracy. Furthermore, transient blade row (time and Fourier transformation) models allow for the simulation of multi-rows, unequal pitch systems using only a few blade passages and less that the full 360-degree geometry.
High Temperature Cooling
Combustion or burning is the sequence of exothermic chemical reactions between a fuel and an oxidant accompanied by the production of heat and conversion of chemical species. The release of heat can produce light in the form of either glowing or a flame.
In a complete combustion reaction, a compound reacts with an oxidizing element, such as oxygen or fluorine, and the products are compounds of each element in the fuel with the oxidizing element. The process releases heat energy.
Other Services
-
Heat Transfer
-
Porous Media
-
Radiation
-
Incompressible & compressible fluid flow
-
Laminar & turbulent flows, transition turbulence modeling
-
Design Optimization Studies for various flow path profiles. (parametric and non-parametric)
-
Non-Newtonian Fluid Models
-
Free form flow path optimization
-
Aero-elasticity and high-Mach
-
Moving Mesh, Morphing Mesh
-
Steady-state & transient flows
-
Supercomputing with MPICH2, MSMPI, and HPMPI on our cluster